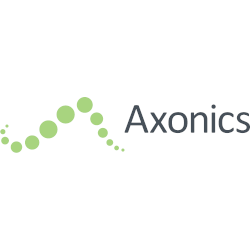
01 Feb Supplier Quality Engineer (SQE)/ Sr. SQE/ PR. QE
Supplier Quality Engineer (SQE)/ Sr. SQE/ PR. QE
Operations and Quality · Irvine, CA · Full time
Job Title: Supplier Quality Engineer (SQE)/ Sr. SQE/ PR. QE
FLSA: Salaried Exempt
Department: Operations and Quality
Reports To: Manager, Quality/ Director, Quality Engineering
To apply, e-mail your resume to careers@axonics.com
Job Responsibilities:
To ensure compliance with the Axonics Quality System, ISO standards, USA FDA, Health Canada, Australia TGA, and other regional requirements, and City, County, State, Fire Marshall and Federal safety regulations. Maintenance and improvement of policies and procedures focused on delivering product and services that are in compliance with company Quality Systems and regulatory requirements.
General Description and Duties:
To perform this job successfully, an individual must be able to perform each essential task satisfactorily. The tasks listed below are representative of the knowledge, skill, and/or ability required to perform this job effectively.
- Quality Systems: Maintain and improve company quality management systems (QMS) in compliance with applicable regulatory requirements related to control of processes, personnel, materials, suppliers, and product.
- Management (Sr. and Pr. SQE only): Responsible for departmental supervision, training, and ongoing support of staff. Required to effectively communicate project goals, project management, and establish staff responsibilities and project tasks. Provide technical guidance and training (mentorship) to less senior staff members to contribute to their ongoing development within the company. May manage supplier audit program and suggest new suppliers to audit.
- Product Development: Is a key member of the product development team representing the Supplier Quality function. Steer and support the design control aspects of product quality, program management, and quality planning from product design through manufacturing. Assess, support and process supplier approvals and re-approvals in the approved supplier list (ASL).
- Process Verification and Validation: Provide input regarding appropriate statistical methods, test methodologies, test facilities and equipment. Coordinate testing and manage resulting documentation. This can include process validation, equipment installation/operational qualification, test method validation, etc.
- Production: May develop and implement quality inspection procedures including sampling plans, for production level components, sub-assemblies and finished goods. May also be responsible for the development and implementation of inspection methodologies, fixtures, measurement systems and calibration of such. Monitor, support and resolve production related quality issues with material suppliers.
- Auditing: Responsible for overall audit program execution. Developing, implementing, and auditing risk-based annual quality control audit plans and schedules. Conduct and lead supplier, internal and external GMP and ISO compliance audits. Supplier quality auditor supports qualification initiatives, continuous improvement, and regulatory compliance across all supplier sites. Reports results and recommendations for changes as required. Confirms acceptable follow up action on audits. Monitors performance to audit schedules, execution, reporting and audit finding closures within established audit plans and timelines.
- Documentation: Create, review, and approve controlled documents on an electronic document control system (e.g. supplier audit plans and reports, nonconformance reports, Quality Manual, work instructions, quality specifications, engineering specifications, lot history and device master records, procedures and validation protocols and reports, etc.). Generate and complete supplier records for approvals in the ASL. Generate, monitor, and complete Manufacturing Quality Agreements (MQAs) based on quality and business risk.
- Training: Coordinates and/or provides training to staff in GMP/ISO, Quality Systems, Supplier Quality, and Safety awareness. Provides ongoing development and maintenance of training materials and records.
- Compliance: Ensures compliance with company quality policies and practices by participating in product and material reviews, assist in “troubleshooting” problems related to the manufacture, testing, validation and documentation. May be responsible for aspects of MRB, corrective actions, process control, complaints, document control, calibration & preventive maintenance programs and product/process/equipment validation activities.
- Regulatory: Facilitate compliance with management strategy and regulatory agencies.
- Product Release: Review and approve lot history records and sterile load records to ensure product compliance with specifications and regulatory requirements. Provide support, guidance, education and training to personnel, ensure inspections, tests, and sterilization is performed in accordance with procedures.
- After Sales Product Monitoring (post-market surveillance): Coordinate attention to customer complaints, corrective actions, Medical Device Reports (MDRs) and product recalls. As required, research and investigate product failures and the reasons for such.
- Logs & Recordkeeping: Ensure compliance of quality related logs and records, including but not limited to CAPA, NCMR, ASL/APSL, equipment CAL/PM, Audit Plan, Report, audit nonconformities (ANCs), and Training.
- Safety: Develop, implement, maintain, and/or inspect required safety programs for flammable, hazardous and bio-hazardous material handling, storage and disposal in compliance with City, County, State, Fire Marshall and Federal safety regulations.
Projects and Other Duties:
- Perform other duties as assigned
Position Qualifications:
- Extensive experience and knowledge of regulatory requirements such as GMP’s, ISO, etc.
- Knowledge of and ability to effectively us analytical tools and methods including statistics, DOE, and the use of computer software packages related to testing, data collection, calibration, etc.
- Strong understanding of medical device manufacturing processes, receiving inspection, in-process and finished device inspections, non-conforming material resolution, CAPA, and record keeping.
- Strong understanding of internal and supplier auditing, process validation, metrology, and inspection equipment.
- Thorough knowledge of applicable City, County, State, Fire Marshall and Federal safety regulations.
- Excellent communication skills (both written and verbal) required.
- Ability to work independently or in team setting required.
- Must be able to travel extensively approximately up to 60%.
Minimum Education:
- MS/BS in Engineering or scientific discipline or equivalent experience
Minimum Experience:
- 3 – 6 years Quality Engineering or auditing role in Medical Device or related industry.
- QE: 2 – 4 years Lead quality auditor. With credentials in Medical Device ASQ CQE/CQA, and/or ISO 13485 auditing certification is preferred.
- Sr. QE: 4 – 6 years Lead quality auditor. With credentials in Medical Device ASQ CQE/CQA, and/or ISO 13485 auditing certification is preferred.
- Pr. QE: more than 6 years Lead quality auditor. With credentials in Medical Device ASQ CQE/CQA and/or ISO 13485 auditing certification is preferred.
Salary:
Aligning our overall business objectives with performance and merit based pay, Axonics offers competitive salaries, performance-based incentives, and Employer paid benefits programs to address the diverse individual needs of our employees and their families. At Axonics, our employees come first!
For California, the base pay range for this position is $86,000 to $145,000 (highly experienced).
The pay for the successful candidate will depend on various factors (e.g., qualifications, education, prior experience).
Axonics is an Equal Opportunity Employer, included protected Veterans and individuals with disabilities.
Please click here to learn more.
No Comments